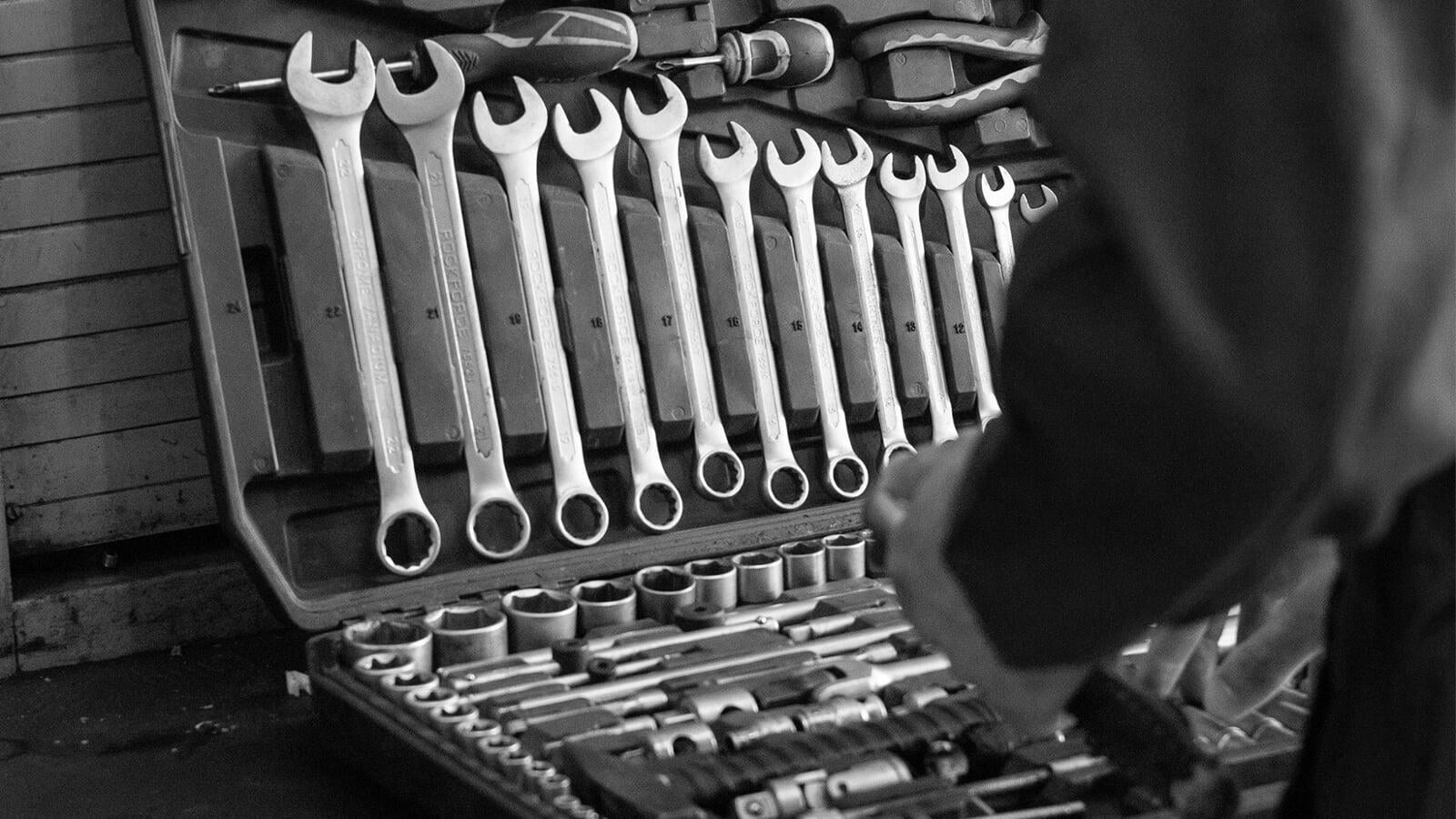
Installation
The first step in installing an environmental test chamber is to select an appropriate site within the facility. Factors to consider include available space, proximity to utilities (electricity, water, gas), ventilation requirements, and access for maintenance. The site should be leveled and free from vibrations or other disturbances that could affect the chamber's operation. If necessary, vibration isolation measures may need to be implemented.
Utilities Connection
Environmental test chambers require connections to various utilities such as electricity, water, and possibly gas or compressed air, depending on the chamber's specifications. A licensed electrician and plumber may be needed to install the necessary wiring, plumbing, and connections according to local building codes and safety standards.
Ventilation and Exhaust Systems
Proper ventilation is crucial to maintain a stable and controlled environment inside the test chamber. This includes providing sufficient fresh air intake and exhaust to prevent the buildup of contaminants or excessive heat. Ventilation systems should be designed to meet the chamber's airflow requirements while ensuring energy efficiency and minimal environmental impact. Safety Features Installation: Environmental test chambers must have safety features in place to protect personnel and equipment. This may include emergency stop buttons, alarms for abnormal conditions (e.g., high temperature, low humidity), and safety interlocks to prevent unauthorized access during operation. Installation of these safety features should comply with relevant safety regulations and standards.
Instrumentation and Control Systems
Environmental test chambers are equipped with sophisticated instrumentation and control systems to monitor and regulate environmental conditions accurately. This includes sensors for temperature, humidity, pressure, and other parameters. The control system may be integrated into the chamber or operated remotely through a computer interface. Calibration and testing of these instruments are essential during installation to ensure accurate measurements. perator
Training
Proper training of personnel who will operate the environmental test chamber is critical for safe and efficient use. Training should cover chamber operation, safety protocols, emergency procedures, and maintenance tasks. Manufacturers or authorized service providers often provide training programs as part of the installation process.
Documentation and Compliance
Detailed documentation of the installation process, including equipment specifications, wiring diagrams, safety certifications, and calibration reports, should be compiled for regulatory compliance and future reference. Compliance with relevant industry standards (e.g., ASTM, ISO) and regulatory requirements (e.g., OSHA, CE marking) is essential for ensuring the chamber's reliability and legal conformity. In summary, the installation capability for environmental test chambers involves a comprehensive process that includes site selection, utilities connection, ventilation design, safety features installation, instrumentation setup, calibration/validation, operator training, and documentation. Proper installation is crucial for achieving accurate and reliable test results while ensuring the safety of personnel and equipment.
Calibration
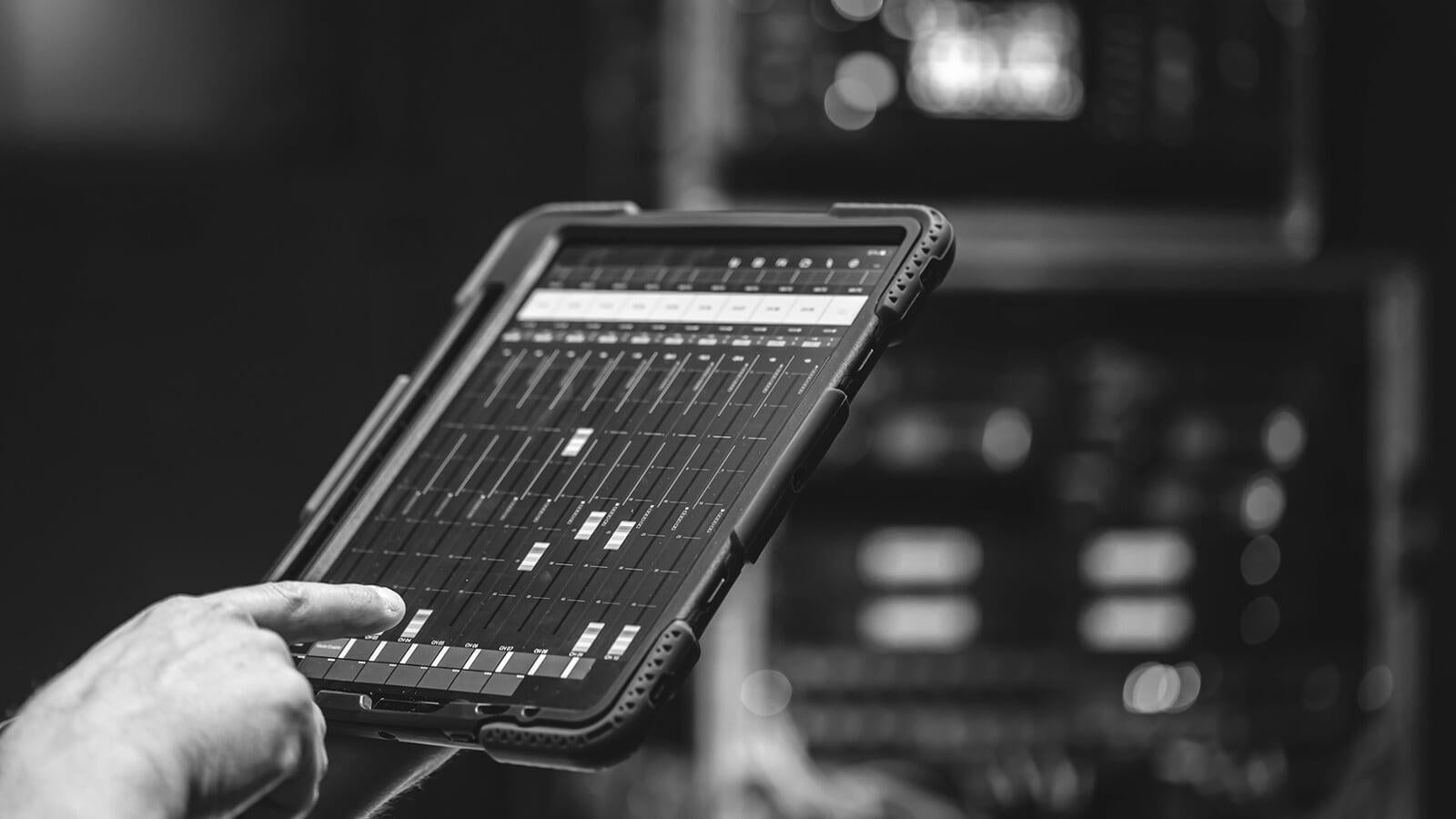
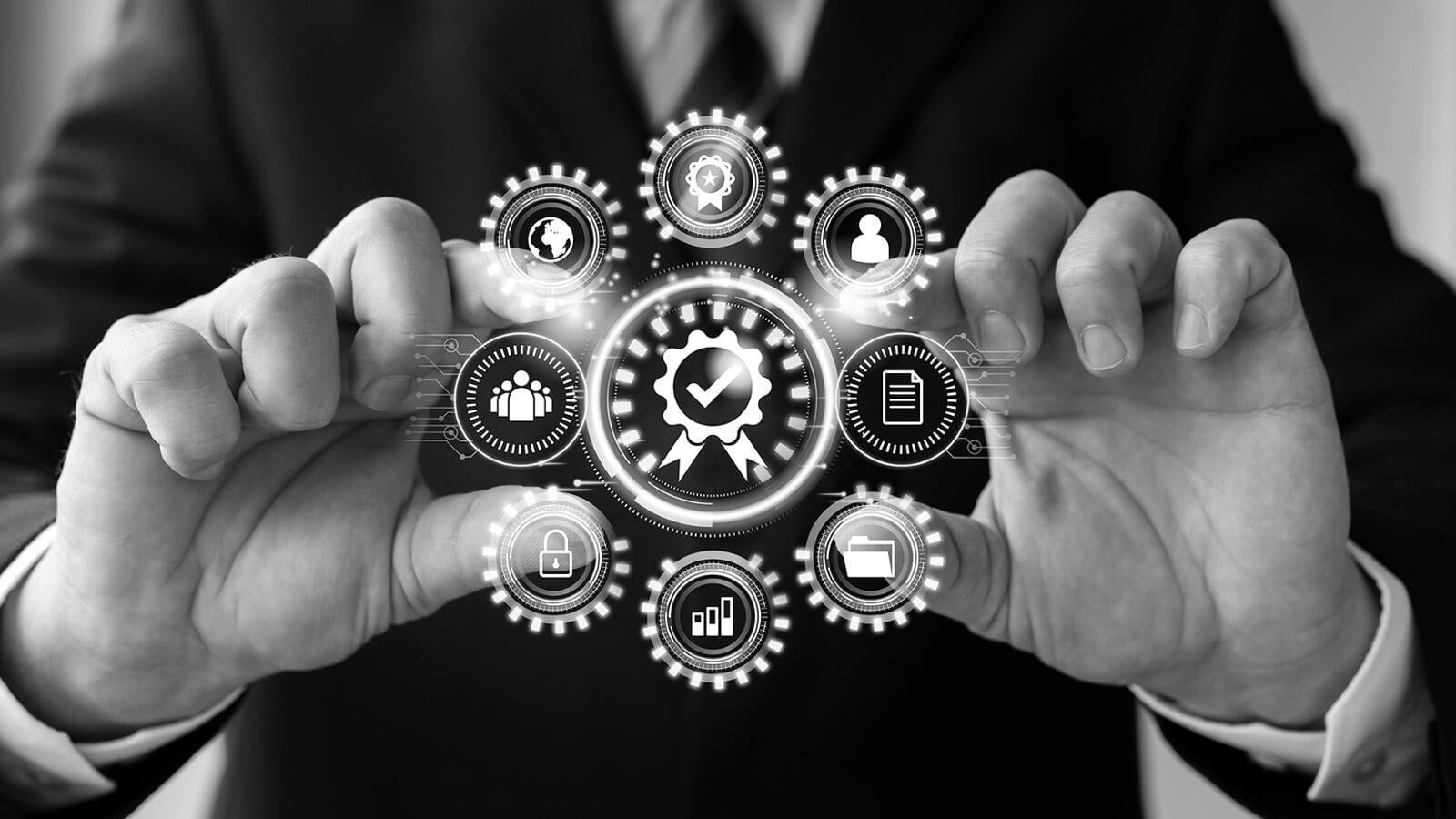
Operational Maintainence
Operational Procedures
Start Up/Shut Down
Proper procedures for starting up and shutting down the test chamber should be followed to prevent damage and ensure safety. This includes activating/deactivating heating/cooling systems, setting desired environmental parameters (temperature, humidity, etc.), and checking for any alarms or abnormal conditions. Test Program Execution: Operating the chamber during test programs involves setting specific test parameters, monitoring environmental conditions, and recording data at regular intervals. Operators should be trained to follow test protocols accurately and respond to any deviations or equipment malfunctions promptly.
Safety Protocols
Operators should be familiar with safety protocols, emergency procedures, and the use of safety features such as emergency stop buttons, alarms, and safety interlocks. Regular safety checks and drills can help maintain a safe testing environment. Calibration and Validation: Maintenance Practices: Scheduled Maintenance: A maintenance schedule should be established for routine inspections, cleaning, and preventive maintenance tasks. This includes checking and lubricating mechanical components, inspecting electrical connections, cleaning filters and vents, and verifying the integrity of seals and gaskets.
Component Replacement
Over time, certain components of the test chamber may require replacement due to wear and tear. This includes heaters, sensors, fans, motors, and control modules. Replacement parts should be sourced from authorized suppliers to ensure compatibility and quality. Troubleshooting and Repairs: Operators should be trained in basic troubleshooting techniques to identify and resolve common issues such as temperature fluctuations, humidity imbalances, or equipment malfunctions. For more complex repairs or technical problems, qualified service technicians may be required.
Data Management
Data Recording
Environmental test chambers generate a significant amount of data during testing. Operators should be trained to record and manage data effectively, including timestamps, environmental parameters, test conditions, and any observations or anomalies. Report Generation: Test reports should be generated upon completion of test programs, summarizing the testing procedures, results, observations, and any deviations from expected outcomes. These reports are essential for documenting test compliance, analyzing trends, and making informed decisions. Operator Training and Certification: Training Programs: Comprehensive training programs should be provided to operators covering chamber operation, maintenance procedures, safety protocols, data management, and troubleshooting techniques. Training should be periodically reinforced to ensure proficiency and update operators on new technologies or procedures.
Certification
Operators may undergo certification or proficiency testing to demonstrate their competence in operating and maintaining environmental test chambers. Certification programs can be conducted internally or by external organizations.
Documentation and Compliance
Maintenance Records
Detailed records of maintenance activities, including dates, tasks performed, parts replaced, and calibration/validation results, should be maintained for each environmental test chamber. These records are essential for tracking equipment history, identifying recurring issues, and demonstrating compliance with regulatory requirements.
Regulatory Compliance
Environmental test chambers are subject to various regulatory standards and guidelines depending on the industry and geographic location. Operators should stay informed about relevant regulations (e.g., ASTM, ISO, CE marking, OSHA) and ensure that testing practices and equipment meet compliance requirements. By implementing robust operational and maintenance practices, environmental test chambers can operate efficiently, produce accurate test results, and contribute to the overall quality and reliability of products and materials tested. Regular training, documentation, and adherence to standards are key elements of a successful operation and maintenance capability for environmental test chambers.
Annual Maintainence
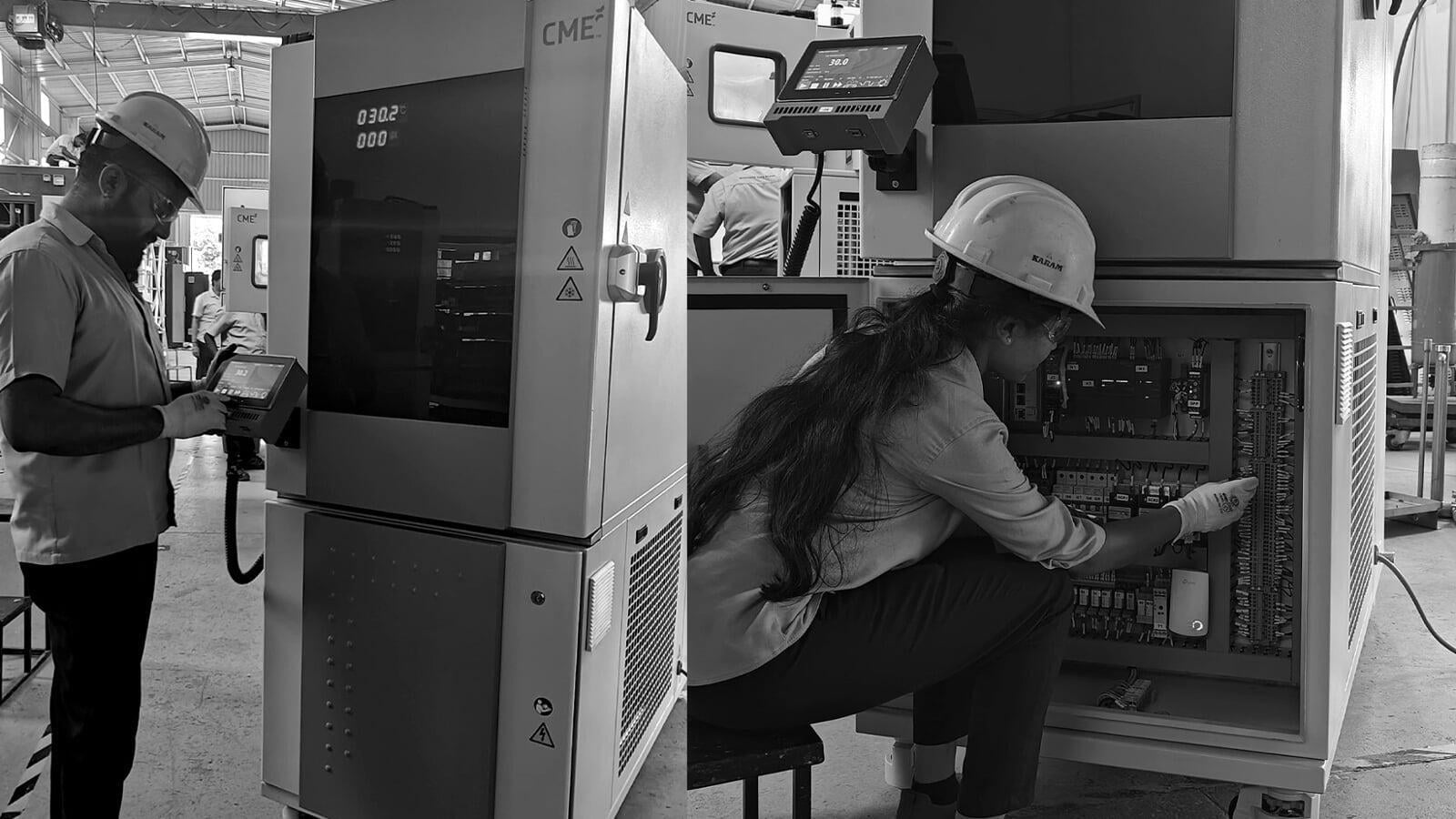
Scheduled Maintenance Visits
(Four Visits)
A. Inspection and Calibration
This visit focuses on a comprehensive inspection of the environmental test chamber to assess its overall condition, functionality, and performance. Tasks include checking electrical connections, inspecting mechanical components (e.g., heaters, fans, motors), verifying sensor accuracy, and testing safety features. Calibration of temperature, humidity, pressure, and other relevant parameters is conducted to ensure accurate and reliable test results. Any minor adjustments or repairs identified during the inspection are addressed to prevent potential issues.
B. Preventive Maintenance and Cleaning
The visit emphasizes preventive maintenance tasks aimed at prolonging the chamber's lifespan and preventing unexpected breakdowns. Tasks may include lubricating moving parts, replacing worn-out components (e.g., filters, gaskets), cleaning internal surfaces, and inspecting insulation for damage. Electrical systems are checked for proper voltage, current, and insulation integrity to prevent electrical hazards. The chamber's ventilation and airflow systems are inspected and cleaned to ensure optimal performance and environmental control.
C. Software Updates and Calibration Verification
During the visit, software updates for the chamber's control system and data logging software are installed to incorporate any improvements or bug fixes. Calibration verification is performed to confirm that the chamber's sensors and control systems maintain accuracy and consistency over time. Data management practices are reviewed, and operators are trained on any new features or functionalities introduced through software updates.
D. Final Checks and Documentation Review
The final check to verify that all maintenance tasks from previous visits have been completed satisfactorily. A comprehensive review of maintenance records, calibration reports, and test logs is conducted to ensure compliance with regulatory requirements and internal standards. Operator training may be reinforced, focusing on best practices for chamber operation, safety protocols, and data management.
Emergency Maintenance Visits
(Two Visits)
A. Immediate Response to Critical Issues
In the event of a critical malfunction or safety hazard requiring immediate attention, an emergency visit is scheduled to diagnose and address the issue promptly. Trained service technicians are dispatched with the necessary tools, equipment, and replacement parts to resolve the problem on-site. The focus is on restoring the chamber's functionality and minimizing downtime to prevent disruptions to testing schedules.
B. Follow-up and Preventive Measures
Following the resolution of the emergency issue, a follow-up visit may be scheduled to ensure that the chamber is operating normally and that preventive measures are implemented to prevent similar issues in the future. Additional training or recommendations for operators may be provided based on the root cause analysis of the emergency issue. Documentation of the emergency visit, including actions taken and lessons learned, is recorded for future reference and continuous improvement.
Documentation and Reporting
Detailed documentation is maintained for each maintenance visit, including checklists, inspection reports, calibration certificates, parts replaced, and any corrective actions taken. Reports summarizing maintenance activities, findings, recommendations, and compliance status are generated and archived for regulatory purposes and internal audits. Data analysis tools may be used to identify trends, track equipment performance, and optimize maintenance schedules based on historical data.
Continuous Improvement and Feedback
Feedback mechanisms, such as customer surveys or feedback forms, may be implemented to gather input from operators regarding the effectiveness of maintenance visits and areas for improvement. Lessons learned from maintenance visits, including root cause analyses of equipment failures or issues, are used to update maintenance procedures, training programs, and equipment design where applicable. Continuous monitoring of chamber performance metrics, such as uptime, reliability, and accuracy, allows for proactive maintenance planning and optimization of resources. By following a structured annual maintenance capability with scheduled visits and provisions for emergency response, environmental test chambers can operate at peak performance, minimize downtime, and contribute to reliable and consistent testing outcomes. Regular maintenance not only ensures compliance with regulatory standards but also extends the lifespan of the equipment, reducing overall operational costs and enhancing productivity.
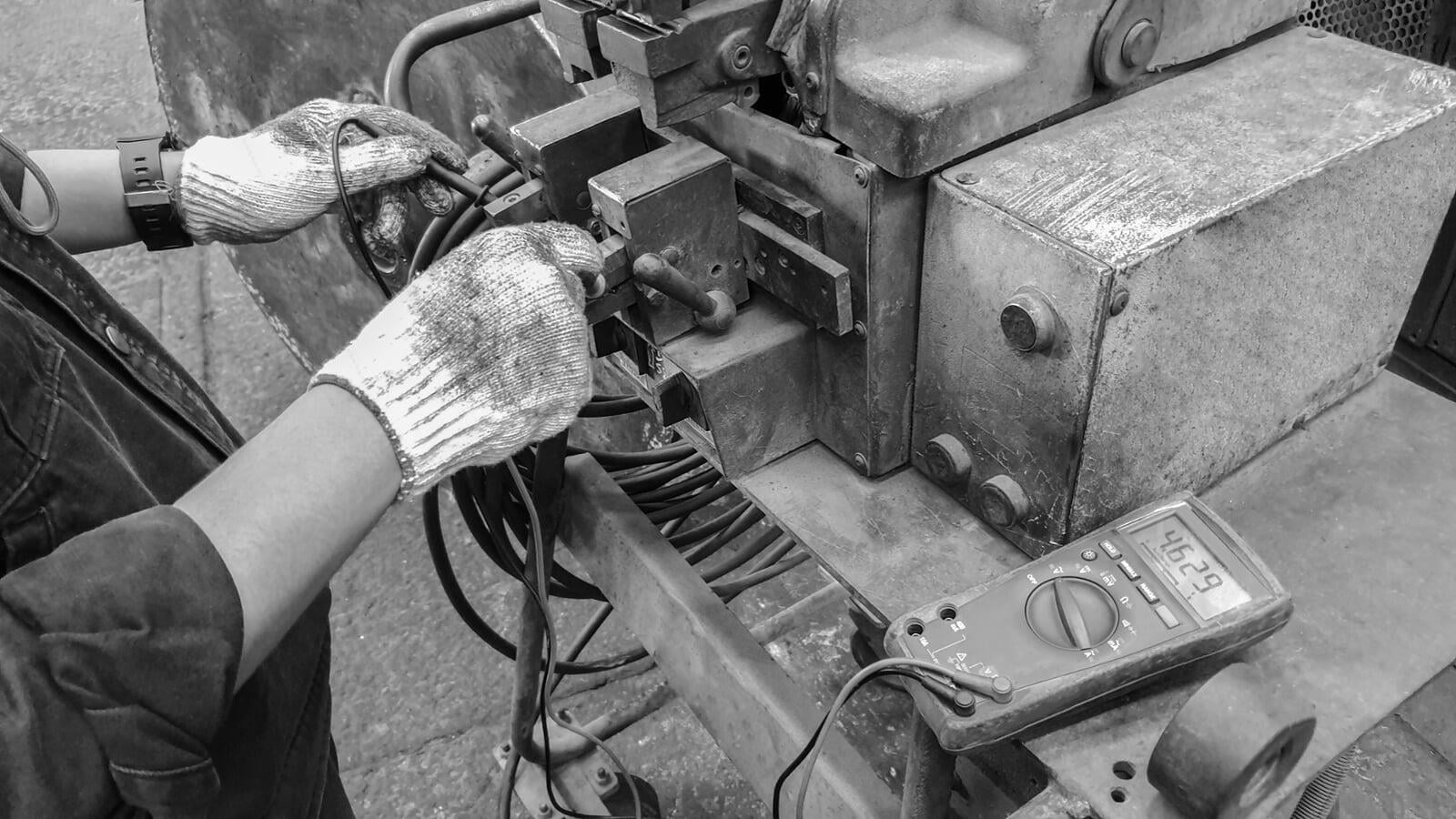
Breakdown Service
Technical Expertise
Mechanical Systems
Skilled troubleshooters understand the mechanical components of environmental test chambers, including heaters, compressors, fans, pumps, and valves. They can diagnose issues related to mechanical wear, component failure, and improper operation.
Electrical Systems
Proficiency in electrical systems is crucial for troubleshooting wiring, circuits, controllers, sensors, actuators, and safety devices. Troubleshooters should be able to identify electrical faults, voltage irregularities, and wiring discrepancies.
Control Systems
Knowledge of control systems, including PLCs (Programmable Logic Controllers), PID controllers, HMI (Human-Machine Interface) panels, and data acquisition systems, enables troubleshooters to address control logic errors, programming issues, and communication failures.
Instrumentation
Familiarity with instrumentation such as thermocouples, pressure transducers, humidity sensors, and flow meters is necessary to troubleshoot sensor accuracy, calibration problems, signal interference, and measurement discrepancies.
Problem-Solving Skills
Analytical Thinking
Troubleshooters should possess strong analytical skills to systematically analyze symptoms, identify root causes, and develop effective solutions. They use logical reasoning and diagnostic tools to isolate and resolve complex problems.
Troubleshooting Methodologies
Knowledge of structured troubleshooting methodologies, such as root cause analysis (RCA), fault tree analysis (FTA), and failure mode and effects analysis (FMEA), guides troubleshooters in systematic problem-solving and decision-making processes.
Critical Thinking
The ability to think critically, evaluate multiple factors, prioritize tasks, and make informed decisions under pressure is essential for resolving unexpected issues and minimizing downtime.
Experience with Environmental Test Chambers
Chamber Operation
Troubleshooters should have hands-on experience operating environmental test chambers, understanding their operating principles, control parameters, test protocols, and safety features.
Previous Troubleshooting
Experience in troubleshooting environmental test chambers equips individuals with insights into common issues, failure modes, maintenance challenges, and best practices for efficient problem resolution.
Industry Knowledge and Standards
Regulatory Compliance
Familiarity with industry standards and regulatory requirements, such as ASTM, ISO, IEC, and NIST, ensures that troubleshooting activities align with quality standards, safety guidelines, and testing protocols.
Safety Protocols
Troubleshooters must prioritize safety by following established safety protocols, using appropriate personal protective equipment (PPE), and understanding potential hazards associated with environmental test chambers (e.g., electrical hazards, chemical exposure, high-pressure systems).
Communication and Collaboration
Effective Communication
Strong communication skills, including clear verbal and written communication, active listening, and concise reporting, facilitate collaboration with team members, operators, engineers, and management.
Collaborative Approach
Troubleshooters work collaboratively with cross-functional teams, including maintenance technicians, engineers, quality assurance personnel, and equipment manufacturers, to leverage collective expertise and resources for problem-solving.
Continuous Learning and Adaptability
Continuous Training
Keeping abreast of advancements in environmental testing technology, maintenance practices, troubleshooting techniques, and industry trends through continuous training and professional development enhances troubleshooters' skills and knowledge.
Adaptability
Troubleshooters must adapt to changing environments, evolving technologies, and new challenges by demonstrating flexibility, resilience, and a willingness to learn from experiences and feedback. Overall, highly skilled individuals who can troubleshoot environmental test chambers possess a combination of technical expertise, problem-solving skills, experience, industry knowledge, effective communication, collaboration abilities, and a commitment to continuous learning and improvement. Their contributions are critical for maintaining the reliability, accuracy, and safety of environmental test chambers in various industries.